Custom CNC Parts Manufacturer: Unleashing Precision in Metal Fabrication
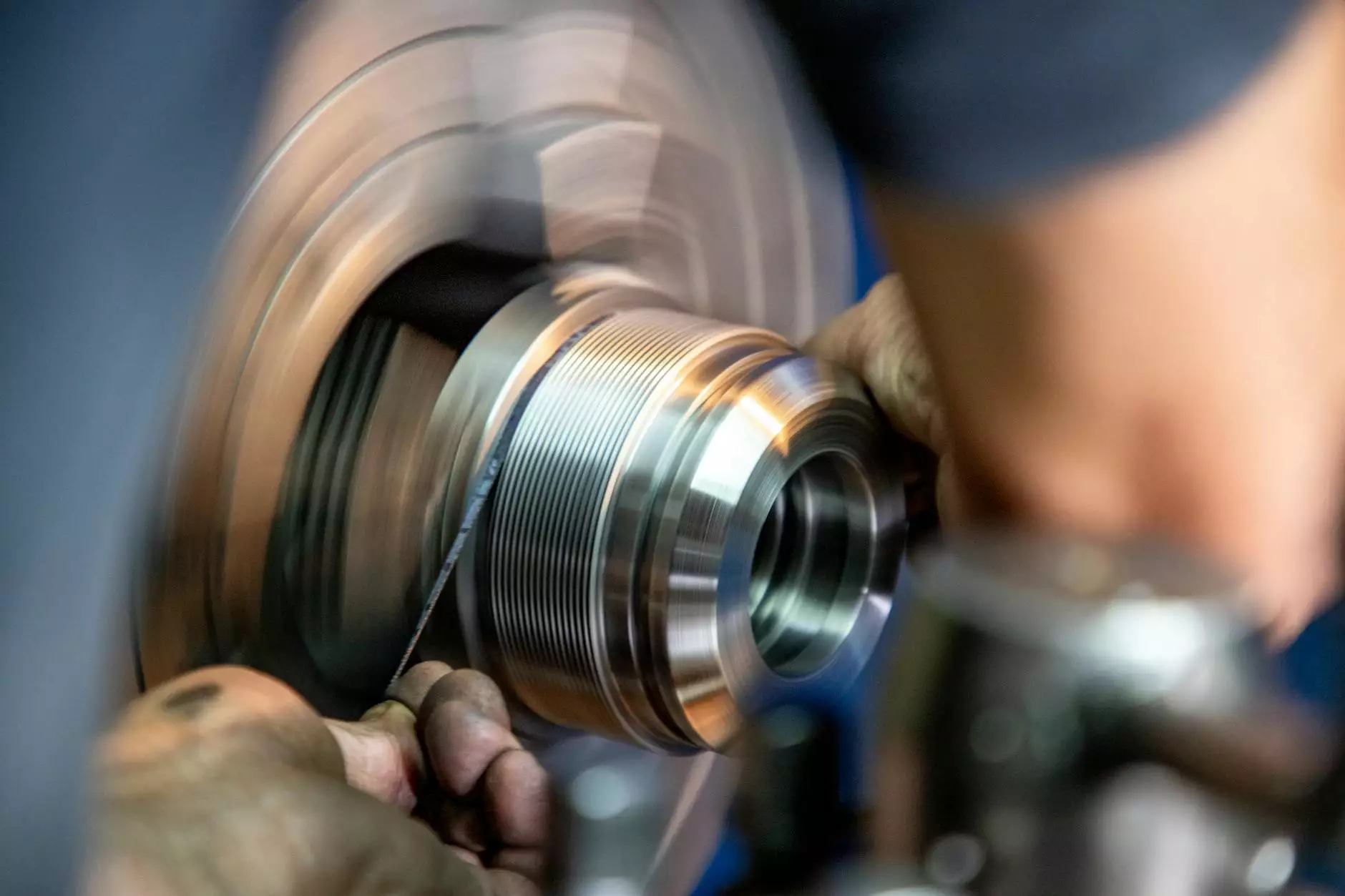
In today's rapidly evolving industrial landscape, businesses are constantly seeking ways to improve efficiency and reduce costs. A critical component of this quest is the use of precision-engineered parts, particularly in sectors where accuracy is paramount. One standout solution in this realm is the concept of a custom CNC parts manufacturer, which plays an essential role in the broader category of metal fabricators. This article explores the significance, advantages, and processes involved with custom CNC manufacturing, particularly from the perspective of DeepMould.net.
Understanding CNC Machining
Computer Numerical Control (CNC) machining is a revolutionary technology that has transformed the way manufacturers produce components. It integrates computer software and machinery to create precise parts from a variety of materials, including metals, plastics, and composites.
The Role of CNC in Precision Manufacturing
- High Precision: CNC machines reduce human error, allowing for intricate designs and tolerances that can be replicated consistently.
- Versatility: A custom CNC parts manufacturer can produce components from a wide range of materials, catering to different industries from automotive to aerospace.
- Efficiency: CNC machines operate continuously and can run indefinitely with minimal oversight, significantly speeding up production times.
- Customization: Users can input specific designs and modifications, allowing for tailor-made solutions for unique applications.
The Importance of a Custom CNC Parts Manufacturer
Choosing the right manufacturing partner is crucial for any business. The advantages of partnering with a custom CNC parts manufacturer are manifold:
1. Tailored Solutions
A custom CNC parts manufacturer can tailor products to meet the precise specifications of their clients. This flexibility leads to components that are specifically designed for particular applications, yielding better performance and enhanced reliability.
2. Cost-Effectiveness
By working with a manufacturer that specializes in CNC machining, businesses can often reduce their overhead costs. CNC processes minimize waste and require less manual labor, which can lower overall production costs significantly.
3. Quick Turnaround Times
Time is often a critical factor in manufacturing. Custom CNC manufacturers, like DeepMould.net, employ advanced technologies and efficient workflows that enable rapid production schedules, ensuring that clients receive their products on time, every time.
4. Enhanced Quality Control
Quality assurance is a cornerstone in manufacturing. CNC machining allows for rigorous quality checks at every stage of production, guaranteeing that each component meets stringent quality standards.
The CNC Machining Process Explained
The process of CNC machining involves several key stages that ensure the efficient production of high-quality components:
1. Design and Prototyping
Using computer-aided design (CAD) software, engineers create detailed digital models of the parts required. These designs dictate every aspect, from dimensions to material specifications.
2. Tool Path Creation
Once the design is finalized, a CNC programmer generates a tool path, which is the sequence of operations the CNC machine will follow to fabricate the part. This ensures optimal efficiency and precision.
3. Machining
The actual machining process begins with the CNC machine cutting the material according to the specifications outlined in the tool path. Depending on the complexity of the part, multiple operations may be required, including milling, turning, and drilling.
4. Finishing
After the machining is complete, finishing processes such as sanding, polishing, or coating may be applied. This step is crucial for enhancing the mechanical properties of the part and improving its aesthetic appeal.
5. Quality Inspection
Finally, rigorous quality checks are conducted to ensure that each component meets the required standards before they are delivered to the client.
Applications of Custom CNC Machined Parts
The versatility of CNC machining means that it has applications across numerous industries. Below are some prominent examples:
Aerospace
In aerospace, components must adhere to extremely high safety standards and precision tolerances. Custom CNC machining allows manufacturers to produce parts that meet these rigorous requirements.
Automotive
The automotive industry relies heavily on custom components for everything from engines to electronic systems. CNC machining enables the production of lightweight yet durable parts that can enhance efficiency.
Medical Devices
In the medical field, precision and reliability are vital. CNC machined parts are often used in surgical instruments and medical devices, where accuracy is not just beneficial but essential for patient safety.
Electronics
The electronics industry requires complex components that can often only be achieved through custom CNC machining. This includes housings, brackets, and other intricate parts that are fundamental for device performance.
Conclusion: The Future of CNC Manufacturing
In conclusion, the role of a custom CNC parts manufacturer is becoming increasingly vital in a world that demands precision, efficiency, and customization. As technology continues to develop, the capabilities and applications of CNC machining will only expand. Companies like DeepMould.net are at the forefront of these advancements, consistently providing high-quality, tailor-made solutions that address the unique needs of various industries.
Getting Started with Custom CNC Parts
For businesses looking to engage with a custom CNC parts manufacturer, it’s essential to take several steps to ensure a smooth process:
1. Identify Your Needs
Clearly define the specifications, materials, and quantities required for your project. Understanding your needs will streamline communication with the manufacturer.
2. Research Manufacturers
Look for manufacturers with proven expertise in your industry. Evaluate their capabilities, past projects, and customer reviews to find a suitable partner.
3. Request a Quote
Once you have selected a manufacturer, request a detailed quote for your project. This should include costs, timelines, and any possible design considerations.
4. Prototype and Feedback
Before full-scale production, ask for prototypes. Provide feedback to ensure that the manufactured parts meet your expectations.
5. Establish a Long-Term Relationship
Building a long-term relationship with your manufacturer can create significant advantages, including improved pricing and faster response times in the future.
Choosing to work with a skilled custom CNC parts manufacturer such as DeepMould.net not only positions your business for greater success but also enhances the overall quality and efficacy of your products. As industries grow increasingly competitive, leveraging technology and precision manufacturing can set your operations apart in a meaningful way.