Design for Additive Manufacturing: Transforming the Future of Business
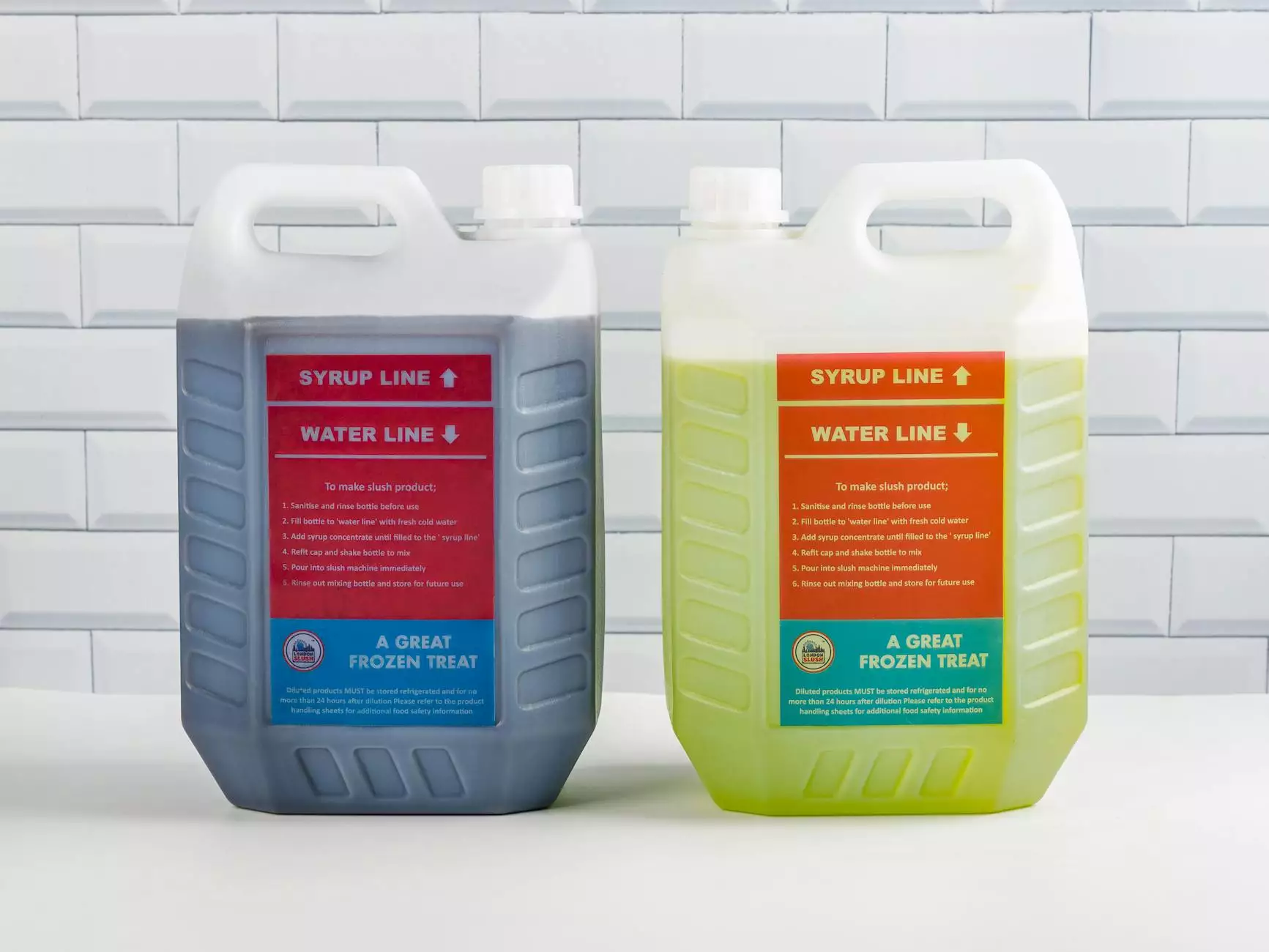
In the constantly evolving landscape of modern business, the need for innovative techniques is paramount. Design for additive manufacturing (DfAM) is one such revolutionary approach that significantly impacts various sectors, particularly in art supplies, product design, and 3D printing. With a focus on creativity and efficiency, DfAM offers businesses an edge in the competitive marketplace.
Understanding Design for Additive Manufacturing
At its core, design for additive manufacturing refers to the practice of designing products specifically for 3D printing. This technique allows for increased complexity, reduced material waste, and the ability to create customized products at a lower cost. DfAM eliminates many limitations associated with traditional manufacturing processes.
The Principles of DfAM
To harness the full potential of DfAM, it’s crucial to understand its foundational principles:
- Complexity is free: Unlike traditional manufacturing, where complexity increases cost, DfAM allows for intricate designs without additional expense.
- Material efficiency: DfAM utilizes only the necessary material, minimizing waste and promoting sustainability.
- Functionality-driven design: Designing with the end-use in mind ensures products are both functional and appealing.
- Customization: DfAM facilitates the creation of unique, personalized products for individual customers or specific applications.
The Role of DfAM in Art Supplies
The art supply industry is beginning to realize the potential benefits of integrating DfAM into their processes. Artists require tools that not only function well but also resonate with their individualistic styles. Through 3D printing, manufacturers can create customized art supplies that cater to specific artistic techniques.
Advantages of DfAM in Art Supplies
Implementing DfAM in the art supply sector leads to numerous advantages:
- Unique Tools: Artists can design and produce tools that align more closely with their techniques, enhancing their creative expression.
- Rapid Prototyping: DfAM enables quicker turnaround times for new products, allowing companies to respond swiftly to market needs.
- Reduced Costs: Outsourcing production for small quantities of specialized art supplies becomes less financially burdensome.
How DfAM Revolutionizes Product Design
Product design is where the transformative power of design for additive manufacturing truly shines. Traditional product design often involves multiple processes, layering in complexity and cost. However, DfAM streamlines this by promoting a more integrated approach.
Efficiency and Speed
With DfAM, the development cycle is significantly accelerated. Designers can swiftly iterate their concepts through the following processes:
- Design Iteration: Quick modifications can be made based on feedback, significantly shortening development timelines.
- Direct Production: Parts can be printed directly from digital files, bypassing the need for molds or assembly lines.
- Integration of Components: Multiple parts can be combined into a single print, reducing assembly errors and time.
Enhancing User-Centric Design
By focusing on the user experience, DfAM enables the creation of products that are tailored to user preferences. This user-centric approach enhances overall satisfaction and aligns products more closely with consumer needs.
Embracing the Future of 3D Printing
As businesses increasingly adopt 3D printing technologies, the importance of DfAM cannot be overstated. The flexibility and versatility of additive manufacturing open up a world of possibilities across industries. From prototypes and end products to art supplies, the application of DfAM is limitless.
Case Studies of DfAM in Action
Several companies have begun to stand out by employing DfAM strategies effectively:
- Custom Footwear: Companies like Nike are using DfAM to create bespoke shoes tailored to individual foot shapes and preferences.
- Aerospace Innovation: Companies in the aerospace sector are utilizing DfAM for lighter, more efficient components that enhance overall performance.
- Healthcare Solutions: Customized implants and prosthetics are developed using DfAM, improving patient outcomes and personalization.
Challenges and Solutions in Implementing DfAM
While the benefits of DfAM are significant, there are challenges associated with its implementation:
Common Challenges
- Complexity in Design: Designing for additive manufacturing requires a shift in traditional thinking, which can be difficult for some manufacturers.
- Material Limitations: Although advances are being made, not all materials are suitable for DfAM processes.
- Initial Investment Costs: High-quality 3D printers and materials can be expensive to acquire.
Effective Solutions
To overcome these challenges, businesses can:
- Invest in Training: Providing team members with proper training on DfAM principles will ease the transition.
- Start Small: By beginning with pilot projects, businesses can test the waters before going all-in on DfAM.
- Collaborate: Partnering with experts in DfAM can provide valuable insights and accelerate learning.
The Future of DfAM and Business Integration
Looking forward, the integration of design for additive manufacturing into business strategies will continue to expand. Trends indicate a stronger push towards sustainability, efficiency, and customization in product development. Businesses that embrace DfAM will likely thrive as they can offer more value to consumers in a world that's increasingly seeking personalization and reduced environmental impact.
Conclusion: The Benefits of DfAM Are Clear
As seen throughout various sectors, the implications of design for additive manufacturing are profound. From art supplies to product design and 3D printing, DfAM is reshaping how products are conceived, developed, and delivered. Companies that harness this powerful tool are not only enhancing their operational efficiency but also opening up new avenues for growth and innovation.
It is imperative for businesses to explore the potential of DfAM now. With the landscape of manufacturing rapidly evolving, those who adapt will lead the way into the future of production. By investing in DfAM strategies, companies can ensure they remain competitive, relevant, and primed for success in an ever-changing market.