Understanding Die Casting: The Role of Die Casting Manufacturers
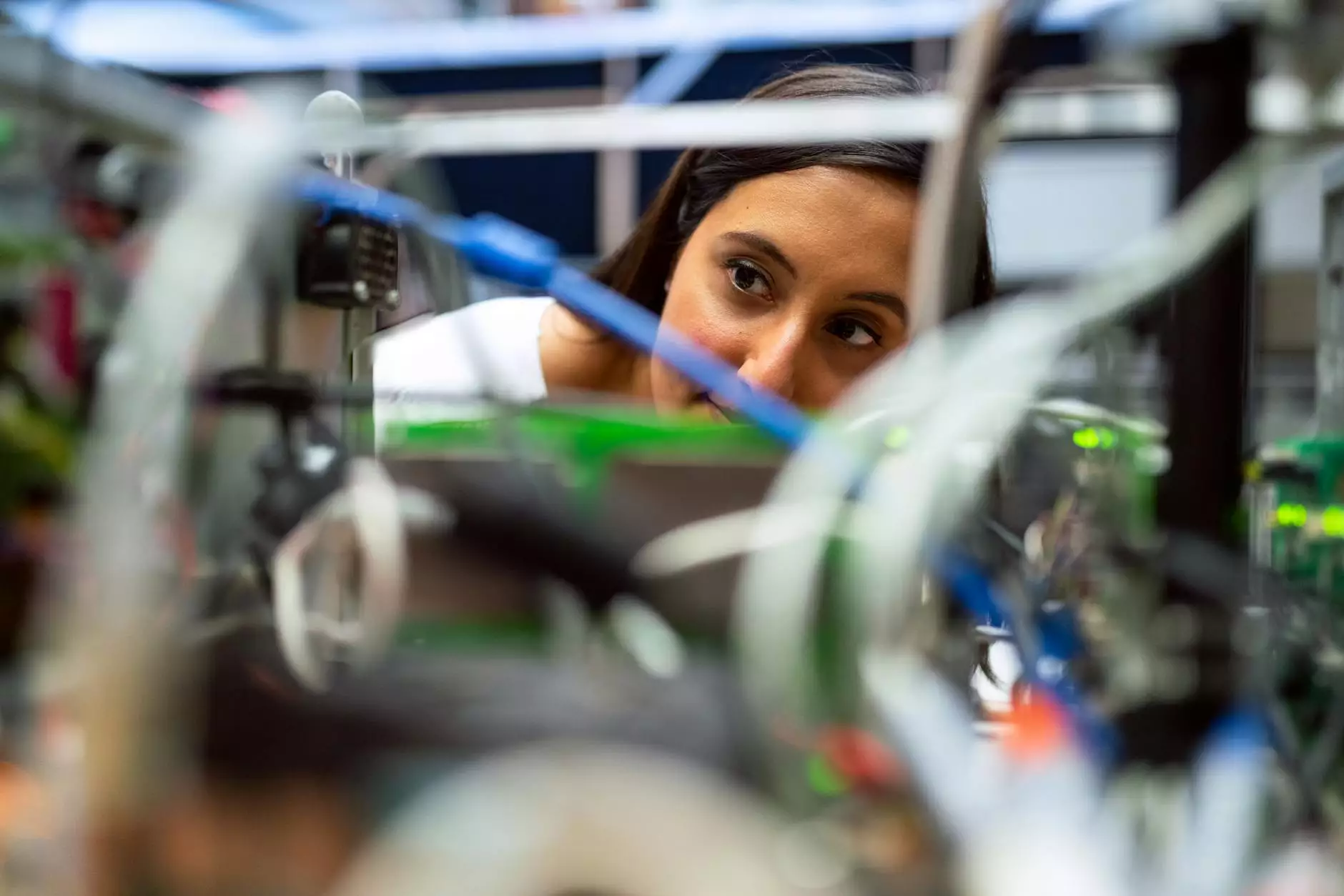
Die casting has become an essential process in the realm of manufacturing, particularly for the production of metal components. A die casting manufacturer plays a crucial role in delivering high-quality precision parts that serve industries ranging from automotive to aerospace, electronics to hardware. This article will delve into the intricate world of die casting, the advantages it offers, the innovative technologies involved, and why you should choose the right die casting manufacturer for your business needs.
What is Die Casting?
Die casting is a manufacturing process that involves forcing molten metal under high pressure into a mold cavity. The mold, usually made from steel, is designed to create parts with intricate shapes and fine details. This process is known for its ability to produce complex geometries which are consistent and repeatable across large production runs.
The Importance of Die Casting Manufacturers
A die casting manufacturer is critical to several sectors, including:
- Automotive: Components such as engine blocks, transmission cases, and various fittings.
- Aerospace: High-strength parts that must endure stringent regulations.
- Electronics: Housings and connectors that require precision and durability.
- Consumer Products: Everyday items such as appliances and tools.
Benefits of Die Casting
There are numerous advantages associated with the die casting process, which contribute to its popularity among manufacturers:
1. High Production Rates
The die casting process is capable of producing high volumes of parts quickly. With the ability to create thousands of parts in a short timeframe, die casting is ideal for large-scale production.
2. Cost-Effective Manufacturing
Due to the high-speed production and reduced need for secondary machining, die casting proves to be cost-effective. The initial investment in high-quality dies pays off when considering the long-term benefits of lower production costs.
3. Excellent Surface Finish
The die casting process often yields a superior surface finish, reducing the need for additional post-processing. The precision of the molds used provides clean and smooth surfaces right out of the process.
4. Complex Geometries
Die casting allows manufacturers to produce complex shapes that would be difficult, if not impossible, to achieve with other methods. This flexibility enables innovation in design and functionality.
5. Material Versatility
While aluminum is the most common material used in die casting, manufacturers can also work with zinc, magnesium, copper, and other alloys, making it highly versatile for different applications.
The Die Casting Process Explained
The die casting process consists of several critical steps:
1. Mold Creation
The first step in die casting is the design and creation of the die, which is a crucial factor affecting the final product. A well-designed die can significantly enhance the quality of the parts produced.
2. Melting the Metal
The selected metal is melted in a furnace until it reaches a molten state, ready for casting. The temperature and alloy composition must be closely monitored for optimal results.
3. Filling the Die
Once melted, the molten metal is injected into the die at high pressure. The pressure ensures that the metal fills every part of the mold, forming the final product accurately.
4. Cooling and Solidification
After filling, the molten metal is allowed to cool and solidify. The cooling time depends on the thickness of the casting and the material used.
5. Ejection
Once solidified, the die opens, and the finished part is ejected. The use of ejector pins often assists in this process to avoid damaging the newly formed part.
6. Trimming and Finishing
Finally, any excess material from the casting process is removed, and the parts may undergo secondary finishing processes, although often, this is minimal due to the exceptional quality of the die casting process itself.
Choosing the Right Die Casting Manufacturer
Selecting the right die casting manufacturer is integral to ensuring the success of your project. Here are several factors to consider:
1. Experience in the Industry
The manufacturer’s experience can significantly impact the quality and suitability of your parts. Look for manufacturers with a proven track record in your specific industry.
2. Advanced Technology
With rapidly evolving technology, a manufacturer who invests in the latest die casting technologies can ensure higher precision, efficiency, and quality in the finished products.
3. Quality Control Processes
Effective quality control is necessary to maintain the standards of the produced components. Inquire about their quality assurance practices and certifications.
4. Customization Capabilities
Every project may require unique specifications. A capable die casting manufacturer should be able to offer customization in designs and solutions tailored to your needs.
5. Competitive Pricing
While cost is essential, it should not compromise quality. Compare the pricing structures of various manufacturers while considering the overall value offered.
Applications of Die Casting in Various Industries
The versatility of die casting allows it to cater to various industries. Let’s explore some specific applications:
1. Automotive Industry
The automotive industry relies heavily on die cast components for structural integrity and weight reduction in vehicles. Parts like gear housings, pump casings, and suspension components are often made using die casting.
2. Aerospace Industry
Aerospace technologies require lightweight and durable components. Die casting is employed to create parts like brackets, supports, and other airframe components that meet strict weight and strength requirements.
3. Electronics Industry
In the electronics sector, heat sinks and casings manufactured through die casting provide necessary thermal management and protection for devices. The precision ensures that connectors and housings function effectively and fit tightly.
4. Medical Devices
Medical equipment manufacturers utilize die casting to produce casings and components that are both lightweight and robust. The need for high standards and reliability makes die casting a reliable choice.
The Future of Die Casting Manufacturing
The die casting industry is experiencing a dynamic transformation driven by technology advancement, sustainability, and the increasing demand for customized solutions. Here are some trends to watch:
1. Automation and Smart Manufacturing
The integration of automation and smart manufacturing solutions is paving the way for increased efficiency and reduced labor costs in die casting processes. This trend is expected to enhance precision and consistency.
2. Eco-Friendly Practices
Sustainability is becoming a focal point for manufacturers. Die casting companies are exploring ways to minimize waste and energy consumption, with innovations such as recycling scrap metal and using eco-friendly lubricants.
3. Advanced Materials
The exploration of new materials and alloys continues to enhance the capabilities of die casting. Manufacturers are experimenting with lighter and stronger materials to meet the needs of various applications.
4. 3D Printing Integration
3D printing technology is beginning to complement traditional manufacturing processes, including die casting. Prototyping and creating complex cores for molds can significantly expedite the development process.
Conclusion
The role of a die casting manufacturer is integral in today’s manufacturing landscape, providing essential components that drive innovation and functionality across various industries. The benefits of die casting, including high production rates, cost-effectiveness, and design flexibility, make it a preferred choice for manufacturers worldwide. When selecting a manufacturer, consider their experience, technology, and commitment to quality to ensure you receive the best outcome for your projects.
For businesses seeking reliable and high-quality die casting solutions, DeepMould stands as a trusted partner, committed to excellence in metal fabrication.