Understanding Die Casting Mold: A Deep Dive into Metal Fabrication
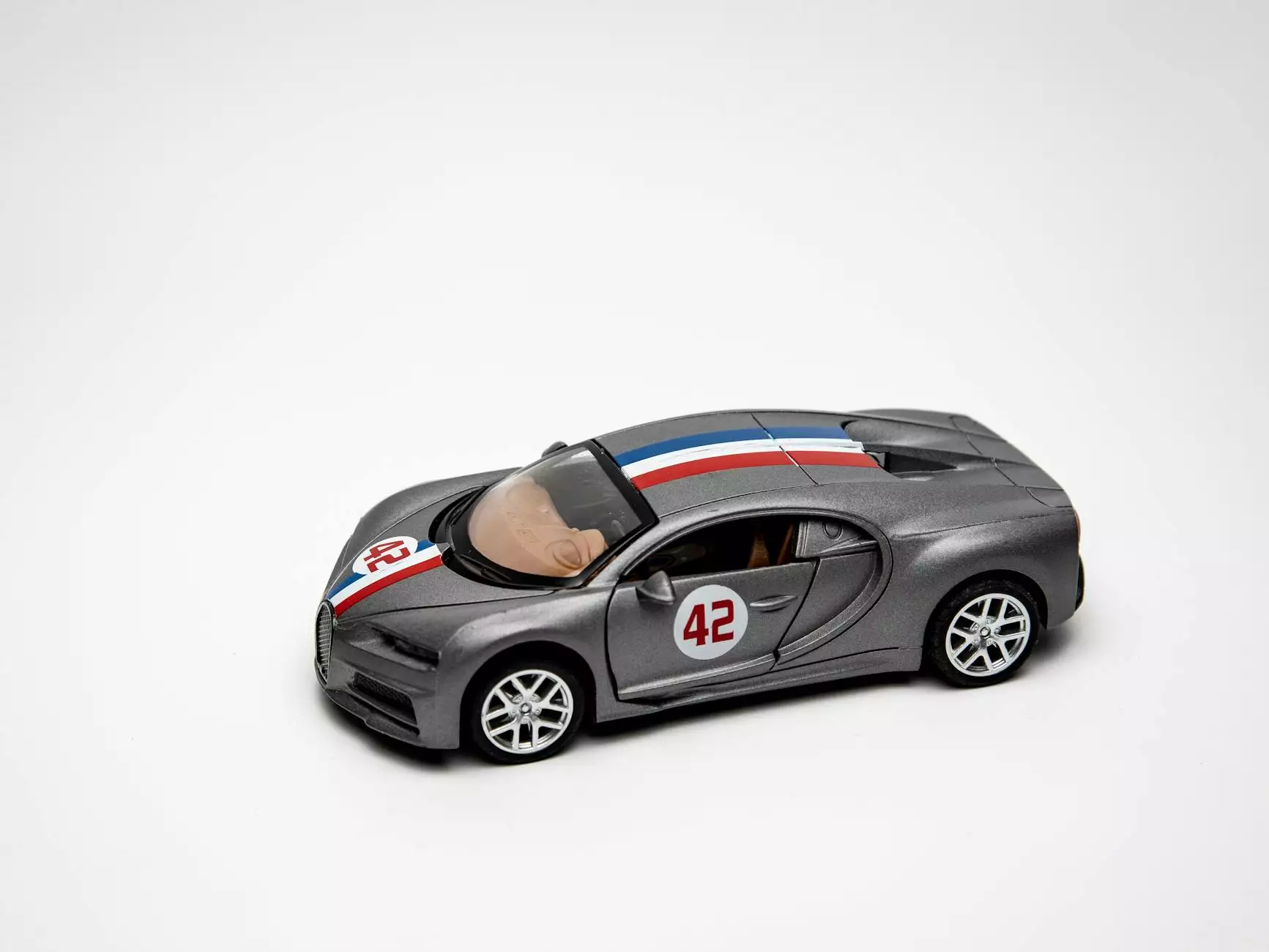
Die casting molds are pivotal in the manufacturing industry, particularly within the metal fabrication sector. These molds play a critical role in shaping and forming various metal components that are essential for numerous applications across diverse industries. In this extensive guide, we will explore what die casting molds are, their advantages, the die casting process, and why choosing the right partner for your die casting needs is crucial. At DeepMould.net, we emphasize the significant role our die casting molds play in enhancing production efficiency and product quality.
What is a Die Casting Mold?
A die casting mold is a tool that is used to form molten metal into specific shapes and sizes. It consists of a two-part cavity that allows the liquid metal to cool and solidify into the desired form. The process involves injecting molten metal into the mold under high pressure, which helps to create precise geometries with excellent surface finishes. This method is particularly effective for high-volume production runs, where consistency and quality are paramount.
The Importance of Die Casting Molds
Die casting molds are essential for creating products that meet stringent tolerances and quality standards. Here’s why they are critical:
- Efficiency: Die casting allows for rapid production cycles, significantly reducing lead times.
- Precision: The process produces highly accurate components, which are crucial for advanced manufacturing applications.
- Durability: Parts produced via die casting offer exceptional strength and longevity due to their metallurgical properties.
- Material Versatility: Various alloys and metals can be used, including aluminum, zinc, magnesium, and others.
The Die Casting Process
The die casting process can be broken down into several key stages, each contributing to the overall effectiveness of the operation. Understanding these stages is crucial for manufacturers and businesses looking to leverage the benefits of die casting.
1. Design and Engineering of the Die Casting Mold
The first step in the die casting process involves the design and creation of the die casting mold. This stage requires collaboration between engineers and designers to ensure the mold meets the specific requirements of the final product. Factors to consider include:
- Mold Material: Common materials used include steel and aluminum, chosen for their thermal conductivity and durability.
- Cavity Design: The cavity shape must be designed to allow for easy filling and to prevent defects.
- Cooling Channels: Effective cooling channels must be integrated to facilitate uniform cooling of the molten metal.
2. Preparing the Die Casting Mold
Once the design is finalized, the mold is fabricated. This process may involve machining, polishing, and applying surface treatments to enhance the mold's performance and longevity. Proper preparation ensures a smooth operation during the metal injection stage.
3. Injection of Molten Metal
In this stage, molten metal is injected into the mold at high pressure. This pressure ensures that the metal fills all cavities of the mold, capturing every detail of the design. The speed of injection and pressure applied are crucial parameters that influence the quality of the final product.
4. Cooling and Solidification
After the molten metal fills the mold, it must be allowed to cool and solidify. The cooling rate affects the metallurgical properties of the finished product. Controlled cooling can reduce residual stresses and improve the overall strength of the component.
5. Ejection of the Finished Component
Once solidified, the mold opens, and ejector pins remove the finished product. This process must be performed carefully to avoid damaging the intricate details of the cast part.
Advantages of Utilizing Die Casting Molds
The choice to use die casting molds offers numerous benefits that can enhance product quality and production efficiency:
- Cost-Efficiency: Though the initial cost of creating die casting molds can be high, the long-term benefits of mass production can lead to significant cost savings.
- Surface Finish: Die casting provides a superior surface finish compared to other manufacturing methods, often requiring little to no additional machining.
- Material Efficiency: The die casting process minimizes waste, ensuring that most, if not all, of the molten metal is transformed into usable parts.
- Complex Geometries: Die casting allows for intricate designs that would be challenging to achieve with traditional metalworking techniques.
Applications of Die Casting Molds
Die casting molds are widely used across various industries. Here are some prominent applications:
1. Automotive Industry
The automotive sector heavily relies on die casting for producing components such as engine blocks, transmission cases, and intricate brackets. Utilizing die casting molds enables manufacturers to produce lightweight yet durable parts that enhance vehicle efficiency.
2. Electronics Manufacturing
In electronics, precise die casting molds are used for producing housings and casings for devices. The ability to create complex geometries helps to accommodate intricate wiring and circuitry.
3. Industrial Equipment
Many components used in industrial machinery and tools are manufactured through die casting. These components require high strength and precision, characteristics that die casting molds excel in providing.
4. Consumer Goods
Die casting is also prevalent in the production of various consumer goods, including household appliances, tools, and decorative items. The ability to produce aesthetically pleasing and functional parts is invaluable in this market.
Choosing the Right Die Casting Partner
Selecting a partner for die casting needs is crucial for achieving the desired results. Here are some considerations to keep in mind when evaluating potential manufacturers:
- Experience: Look for a manufacturer with a proven track record in die casting and an understanding of your specific industry needs.
- Quality Assurance: Ensure that the company has rigorous quality control processes in place to guarantee consistency and reliability in products.
- Technology: Advanced technology and equipment can significantly enhance the die casting process. Choose a manufacturer that invests in modern techniques and equipment.
- Support Services: After-sales support, including troubleshooting and maintenance services, is vital for maintaining the longevity of your die-cast products.
Conclusion
In conclusion, die casting molds are an indispensable tool in the realm of metal fabrication, providing unmatched advantages in efficiency, precision, and quality. With the right partner, such as DeepMould.net, businesses can leverage the full potential of die casting to meet their manufacturing needs. By investing in high-quality die casting molds, companies can not only enhance their production capabilities but also ensure a competitive edge in the fast-evolving market landscape. Embrace the future of manufacturing with die casting and take your business to new heights!